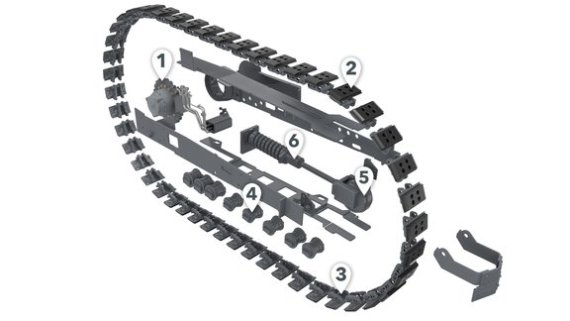
Undercarriage crawler drive
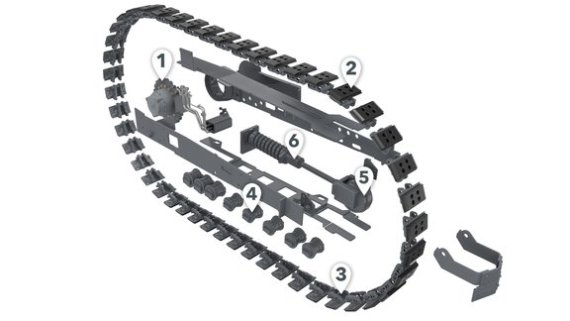
Undercarriage parts
All components are matched so that the machine provides a high degree of traction and operational reliability while minimising application-related wear and tear. Whether it is application-related wear or improper maintenance that causes problems: excessive wear of components or damage to individual parts leads to unplanned machine breakdowns on the construction site.
Undercarriage components, particularly those involved in active functions, endure ongoing operational stress, resulting in wear and component fatigue over time. Through long-standing collaboration between our suppliers and the design teams at our primary factories, undercarriage components are meticulously harmonized. This careful matching ensures that the machine delivers optimal traction and operational reliability while minimizing wear and tear associated with specific applications. Whether it's wear due to specific applications or inadequate maintenance that poses issues, excessive component wear or damage to individual parts can result in unplanned machine breakdowns at construction sites.
Wear and tear on chassis components
Reasons and maintenance tips
Every component in tracked machinery experiences varying degrees of wear and tear. The underlying causes are multifaceted, and while wear can be postponed, it can only be prevented within specific parameters. Factors such as contamination, improper installation, or the utilization of components from different manufacturers not only impact the machine's performance but can also accelerate wear in other components.
The most common causes of undesirable wear behaviour include:
- sticking and clumping of milling dust or asphalt residue (insufficient cleaning);
- high speeds when "transferring" from one section to another;
- frequent use of reverse gear;
- chain tension is too loose;
- abrasive materials (sand, milling dust, etc.) on the sliding or rolling surfaces.
What is wear and tear and how to avoid it
Wear arises from the contact pressure between two elements in relative motion, resulting in the detachment of minuscule particles from their surfaces. Contamination exacerbates this wear process, with abrasive substances like sand infiltrating all contact points, notably diminishing the longevity of chassis components. Therefore, consistent cleaning and maintenance are essential for achieving maximum service life.
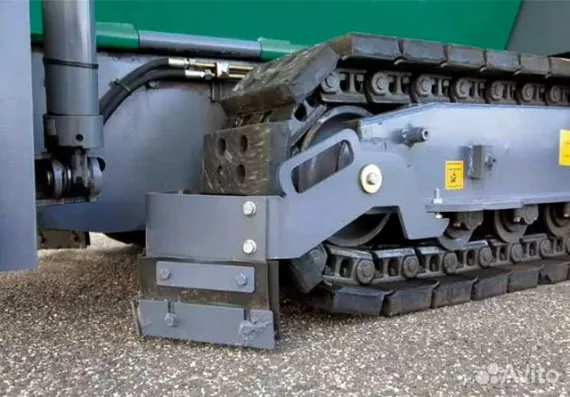
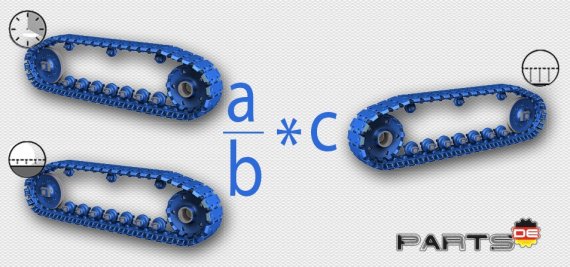
Formula for calculating the service life of wearing parts
Utilize the provided calculation formula to forecast the service life of a wear part in the undercarriage area with precision.
For instance, in calculating the wear of a running gear shoe (represented by dimension W1), consider the following:
The wear height of the EPS pads after 750 operating hours is approximately 40%, equating to a measured height of 43.2 mm. Using these figures, you can estimate the service life of the shoe under identical wear conditions.
750 hours / 40% (*) x 100% (**) = 1875 hours
Hence, the projected service life until replacement of this EPS pad amounts to 1875 hours.
(*) The percentage of wear can be derived from the comparison tables in the relevant sections. (**) Typically 100%, as surpassing this value in most cases results in severe damage to other components.
For our customers, this calculation formula offers an estimated value to assist in scheduling proactive maintenance for WIRTGEN Group machinery, ultimately extending their operational lifespan. Alterations in influential factors, including contamination levels, component damage (like cracks or chips), and maintenance intervals, can impact the outcome. It's important to note that the percentage wear condition is a momentary measurement, subject to change during the wear part's usage, potentially leading to an adjustment in the projected service life, either reducing or increasing it.
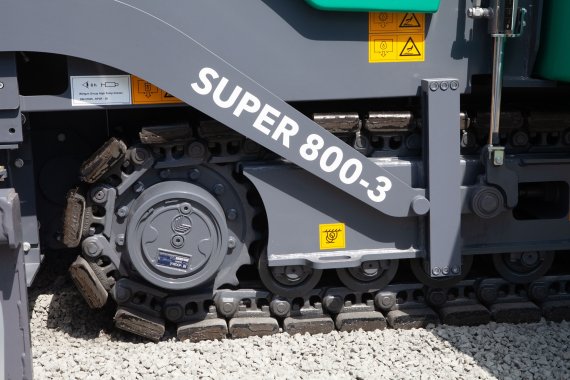